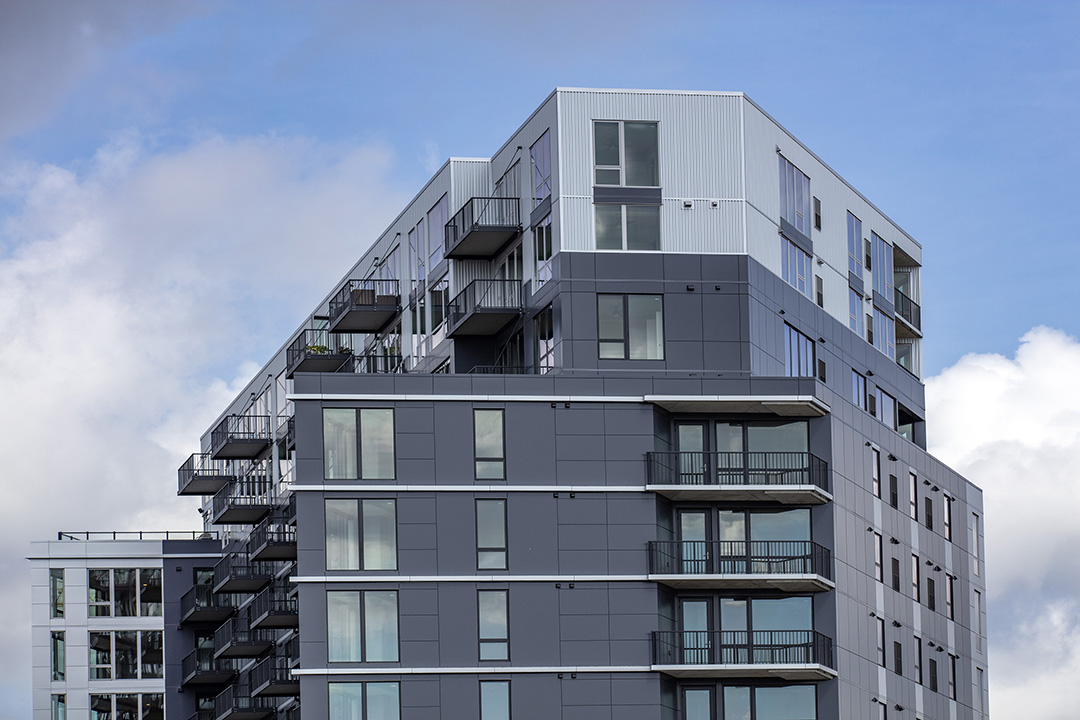
The new Ironclad mixed-use development in Minneapolis stands out in the historic Mill District’s cityscape with a unique metal-clad angular design that is equal parts historic inspiration and contemporary urban chic.
Highlights
• Ironclad is comprised of the 14-story 171-unit Ironclad apartment building featuring high-end amenities and the eight-story 148-room millennial-focused Moxy Minneapolis Downtown hotel by Marriott International.
• Ironclad was constructed on the site of The Union Grain Elevator or Elevator E, which was constructed in 1867 as one of Minneapolis’ earliest and largest (130,000 bushel capacity) wood grain elevators, according to a Collage Architects’ statement.
• Collage Architects selected ALUCOBOND PLUS in the Custom French Beret Lighter color with an understated purple hue to subtly mark the passing of Minneapolis’ own “Purple Rain” singer-songwriter Prince.
Project: Ironclad
Location: Minneapolis, MN
ALUCOBOND® PLUS: Custom French Beret Lighter, Brilliant Silver Metallic
Architect: Collage Architects, LLC
General Contractor: Kraus-Anderson Construction Co.
Fabricator/Installer: Berwald Roofing & Sheet Metal Co., Inc.
Photography: © Bob Perzel
The Project
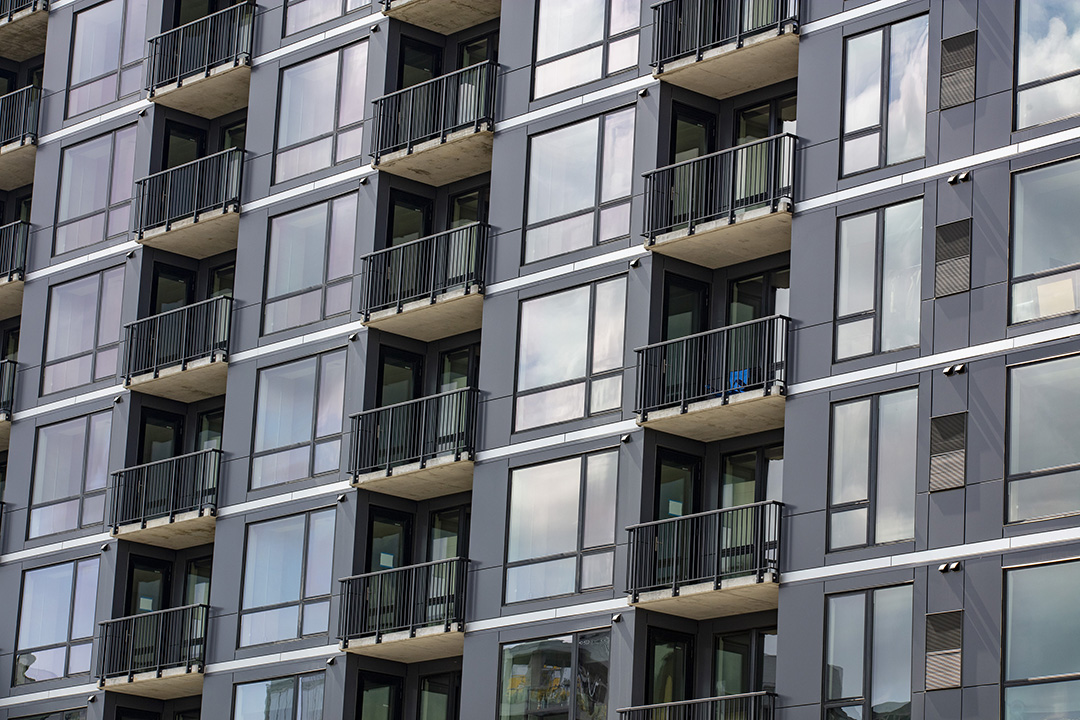
Designed by Minneapolis-based Collage Architects, LLC, this $74 million 418,864 square-foot development opened in July 2019 in the city’s fast-growing East Town Neighborhood. Ironclad is comprised of the 14-story 171-unit Ironclad apartment building featuring high-end amenities and the eight-story 148-room millennial-focused Moxy Minneapolis Downtown hotel by Marriott International. Ironclad also features 8,900 square feet of retail space with a premiere anchor restaurant scheduled to open in winter 2020. Parking is available for 400 cars in a garage designed with two stories above ground and 1.5 stories below.
Ironclad is owned by Minneapolis-based Timeshare Properties, Inc., which owns and operates multiple properties in downtown Minneapolis. The Moxy Minneapolis Downtown hotel is managed by Minneapolis-based Graves Hospitality Corp.
Located at the intersection of Chicago and Washington avenues – within walking distance of U.S. Bank Stadium, Gold Medal Park and the Guthrie Theater – Ironclad was constructed on the site of The Union Grain Elevator or Elevator E, which was constructed in 1867 as one of Minneapolis’ earliest and largest (130,000 bushel capacity) wood grain elevators, according to a Collage Architects’ statement. The elevator was located on the Chicago, Milwaukee and Saint Paul railway that ran toward the Mill District along the Mississippi River. Prone to fire, the original wooden elevator burned to the ground in 1892. It was reconstructed and “iron clad” to better protect the structure against future fires. Today, the only visible reminder of the site’s historical importance is the stone wall that supported the railway viaduct.
Design
The Ironclad mixed-use development pays homage to its historic industrial namesake with construction materials that include reinforced concrete and brick. Today’s Ironclad is clad in a total of 99,170 square feet of ALUCOBOND® PLUS aluminum composite material (ACM) by 3A Composites USA, including 65,410 feet of 4mm ALUCOBOND PLUS in the Custom French Beret Lighter color and 33,760 square feet of 4mm ALUCOBOND PLUS in the Brilliant Silver Metallic color from The Classic Collection.
(As the original aluminum composite material, ALUCOBOND PLUS has been developed exclusively to allow architects and designers to meet the fire performance requirements of today’s building standards. Consisting of two sheets of smooth .020” aluminum thermobonded to a solid, fire-retardant core in 4mm nominal thickness, ALUCOBOND PLUS is one component of the wall assembly that meets the requirements of fire classifications while offering the proven product properties such as flatness, formability, durability and ease of fabrication. Available in standard widths of 50 inches and 62 inches, ALUCOBOND PLUS is available in a wide range of high quality finishes and colors as well as custom colors.)
Collage Architects sought to retain the site’s historical significance for the city by including the railway’s stone retaining wall boulders as part of the Ironclad development’s landscape, according to Joshua Jansen, Associate AIA, Vice President and Director of Design at Collage Architects.
“The only remaining visual signs of the grain elevator were the stone and the peculiar shape of the site driven by the historic railway, so we decided to design the building with an angular shape to emulate the old elevator,” said Jansen. “Our building is much more angular than every other building that fronts Washington Avenue and has a piece that juts out to take on the old form of the elevator that you can actually walk beneath. … This building needed to have an energy in the same way as the old Elevator E. We wanted this design to be imposing, impactful and incorporate high design, while strengthening the public realm along Washington and Chicago avenues.”
Collage Architects sought to preserve the visual corridor between U.S. Bank Stadium and the Guthrie Theater not only in its design of Ironclad but in its selection of cladding materials, according to Jansen. He said the color of brick was chosen to clad the Moxy hotel in order to emulate the broader site’s history, while the Ironclad apartments were clad in modern ALUCOBOND PLUS ACM to reflect the “edginess” of the stadium, the Guthrie and the evolving Washington Avenue corridor.
“We utilized the ALUCOBOND PLUS to create a unique color and form in the cityscape,” said Jansen.
Collage Architects selected ALUCOBOND PLUS in the Custom French Beret Lighter color with an understated purple hue to subtly mark the passing of Minneapolis’ own “Purple Rain” singer-songwriter Prince. In order to match the architects’ vision, 3A Composites USA produced several custom ALUCOBOND PLUS color samples, which Jansen took to the site to assess their compatibility with the nearby stadium.
While the main body of the building is clad in Custom French Beret Lighter, ALUCOBOND PLUS ACM in Brilliant Silver Metallic was installed as vertical and horizontal accents at floor lines. “We selected the silver color as an obvious cue from the stadium,” said Jansen. “We wanted to reflect the energy of the historic rail line and the new stadium.”
The Ironclad apartments feature floor-to-ceiling windows and stacked units – a design that “required a cladding material that had a lot of control in its seaming pattern to maintain the lines of the building,” according to Jansen, who said the intersections of these materials are very sharp.
“The ALUCOBOND PLUS material created these clear lines; it worked great,” said Jansen. “We had, of course, used it before but never on such a large project. This project’s scale and its impact on the city required a premium product.”
Fabrication and Installation
Approximately 4,012 ALUCOBOND PLUS panels were fabricated and installed on Ironclad by Berwald Roofing & Sheet Metal Co., Inc., of North St. Paul, Minn., with a Berwald rainscreen dry-set panel system. Minneapolis-based Kraus-Anderson Construction Co. served as general contractor for the project.
The ALUCOBOND PLUS material was sold by EBP, LLC, of Excelsior, Minn. Berwald Roofing & Sheet Metal served in a design-assist role on the project, reviewing and documenting wall assemblies not only to bring the architect’s vision to life but to meet building codes in Minneapolis and Minnesota, according to Brian Berwald, General Manager, Berwald Roofing & Sheet Metal Co., Inc.
Berwald said fabrication and installation of the ALUCOBOND PLUS and other metal panel materials was completed on a “very tight time schedule for the size of the project” from August 2018 through May 2019, including working around a month-long construction closure during the spring 2019 NCAA Division I Men’s Basketball Tournament held at nearby U.S. Bank Stadium.
Berwald Roofing & Sheet Metal team members were challenged in installation by the unique angles in Ironclad’s design, including a solid wall of panels found on the east side of the apartment building facing Washington Avenue that turns at a 150-degree angle, according to Berwald.
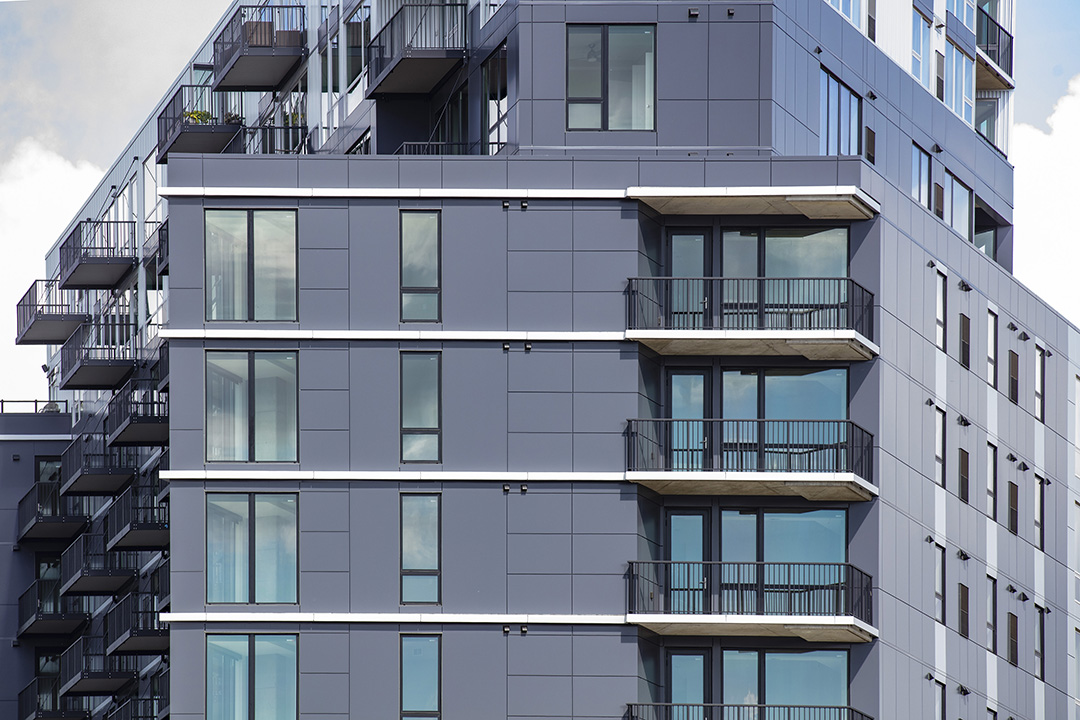
“The panels at that location come across the building and turn back at a tight angle with one-piece mitered corners,” said Berwald. “All of the ALUCOBOND PLUS panels had to line up correctly around the entire building. We paid close attention to the design and shop drawings to make this work.”
Now that Ironclad has opened, this unique design has paid off in praise, according to Jansen, who said he’s been told by competitive peers in the architectural community that this is “a great addition to the city.”
“Everyone thinks this building looks great,” said Berwald. “It’s located on a perfect spot on Washington Avenue and really stands out.”
Jansen recently led a discussion and tour of the Ironclad development for neighboring business owners and real-estate developers.
“We discussed how the angles and the history and the ALUCOBOND PLUS product all work together to create the unique flavor of this project,” said Jansen. “People on the tour started asking a lot of questions about the angles because we so often see these developments designed to maximize square footage. They were impressed that you can walk under the part of this building that connects Washington Avenue to Ninth Avenue and the expansive Hiawatha Bike Trail. This is such an unusual site within the city grid; its design centers on the push and pull of the building and the importance of historical context.”
Introduced in 1969, ALUCOBOND is the original and world’s best-known aluminum composite material. ALUCOBOND PLUS is manufactured in the United States in the Benton, Ky., plant of 3A Composites. The 3A Composites USA headquarters are based in Davidson, N.C. For more information about ALUCOBOND PLUS ACM, call 1-800-626-3365, email info.usa@3AComposites.com or visit www.alucobondUSA.com.