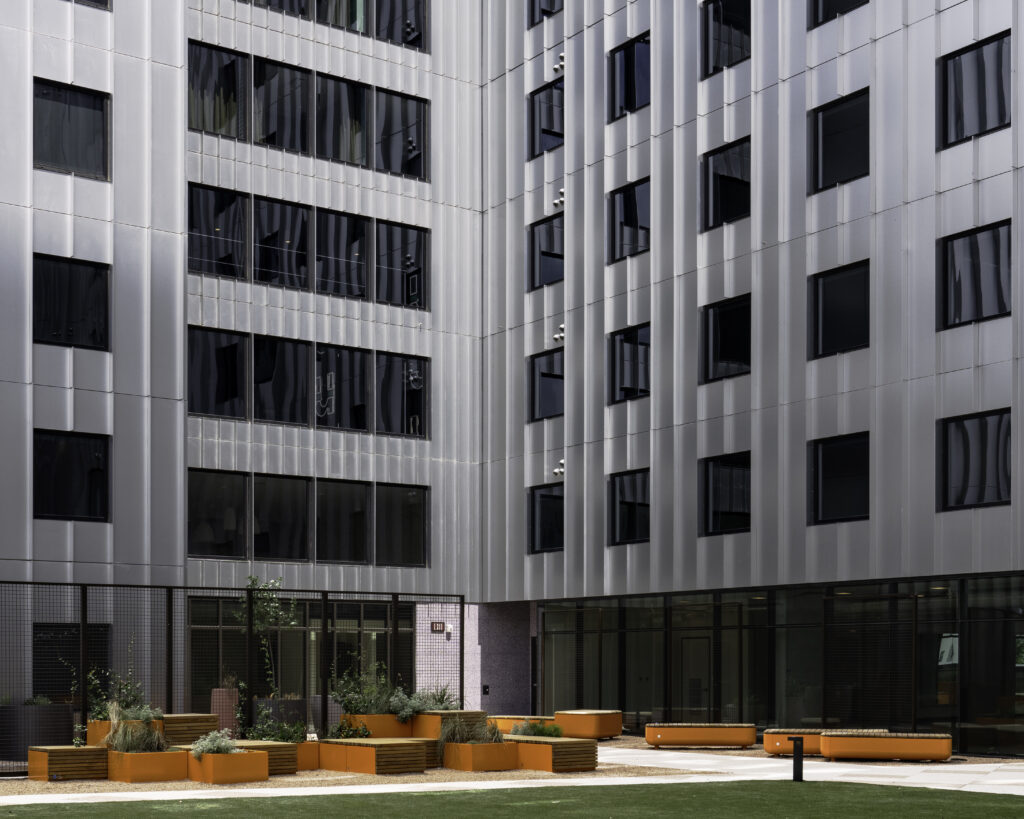
The commercial building industry is changing rapidly. Architects, developers, builders, contractors and fabricators are searching for innovative – and cost-effective – solutions that will enable them to work quickly and safely while still delivering high-quality, sustainable finished projects. One such solution is prefabricated (“pre-fab”) construction, a method that helps to streamline the building process and produce beautiful results.
In commercial building, pre-fab construction of a building’s façade typically involves assembling, in a controlled environment, large exterior panels into units. The completed units — which can be larger than 40 feet wide and a story tall — are then transported to the job site. Once on-site, they are connected to the building’s structure.
This method is challenging traditional paradigms in commercial construction, creating value by offering design flexibility, faster project delivery and accelerated project scheduling, quality assurance and reduced risk of jobsite injuries.
Top Six Reasons to Choose Pre-fab Construction and ALUCOBOND® PLUS
1. Architectural Freedom and Flexibility
Pre-fab provides architects with the opportunity to explore creative and intricate designs that may otherwise present challenges for installers on a traditional construction site. Gone are the days of pre-fab being synonymous with uninteresting flat box building designs. Advancements in technology and craftsmanship have propelled this construction method into the spotlight. Architects can now create stunning, original buildings leveraging the flexibility offered by pre-fab to create unique and aesthetically pleasing facades that are meticulously constructed in a managed environment. By pairing this approach with the nearly-unlimited range of ALUCOBOND PLUS colors and finishes, architects can see their design intent come to life and developers can quickly have their eye-catching projects completed and occupied.
2. Efficiency in Design Implementation
Both Computer Assisted Design (CAD) and Building Information Models (BIM) software are commonly utilized in pre-fab construction, allowing architects to pre-program sophisticated design details, streamlining the design implementation process for specialty contractors building pre-fab wall panels. Design adjustments can be easily managed in the controlled environment of a shop, reducing the need for last-minute jobsite modifications. By specifying highly-formable ALUCOBOND PLUS on pre-fab exterior wall panels, architects are able to incorporate dimensional panels and complex design elements into their projects.
3. Quality and Predictability
One key advantage to pre-fab construction is its predictability. Not subject to delays caused by weather or other outside elements, pre-fab shop crews are able to complete highly-repetitive work with greater efficiency, consistency and precision. Fully constructed in a climate-controlled shop, production schedules are strict and finished panels are delivered in a timely fashion, leading to quicker project completion.
4. Safety and Risk Mitigation
Pre-fab construction reduces the risk of common on-site injuries associated with a traditional construction method. Each panel is completely finished before arriving at the jobsite, allowing builders and developers to rest easier knowing that there are a limited number of workers engaged at heights or subject to the chaos that can take place on a construction site.
5. Cost-Effective Project Management
Pre-fab construction provides an accelerated alternative to the traditional stick building approach. Homing in on the critical path of the construction schedule — the dry-in phase — the pre-fab method means that while a building’s infrastructure is being framed, the offsite specialty contractor is fabricating the wall panels in tandem. Once the structure’s framework is complete, the pre-fab panels are transported and lifted into place, expediting the cladding of the building. This dries in the building faster allowing the interior trades to begin sooner and ultimately leads to faster project turnover and improved financial outcomes for the stakeholders.
“Pre-fab construction is a reliable solution for ensuring that projects are executed with precision and on time,” said Sam Balunda, executive vice president, Baker Triangle. “In construction, every moment counts, and this approach optimizes both time and resources.”
The time efficiency advantage of pre-fab construction is directly tied to profitability for building owners whose assembly process equates to revenue. This is especially true in the development of multi-family, student housing, healthcare facilities and hospitality.
6. Sustainability
Unlike traditional construction methods that involve a wide variety of vehicles repeatedly commuting to various job sites, pre-fab construction centralizes the assembly process to a single worksite where the panels are assembled. This single assembly point reduces transportation, minimizing the impact of energy consumption and pollution, and lowering the overall carbon footprint, making pre-fab construction an environmentally-conscious choice.
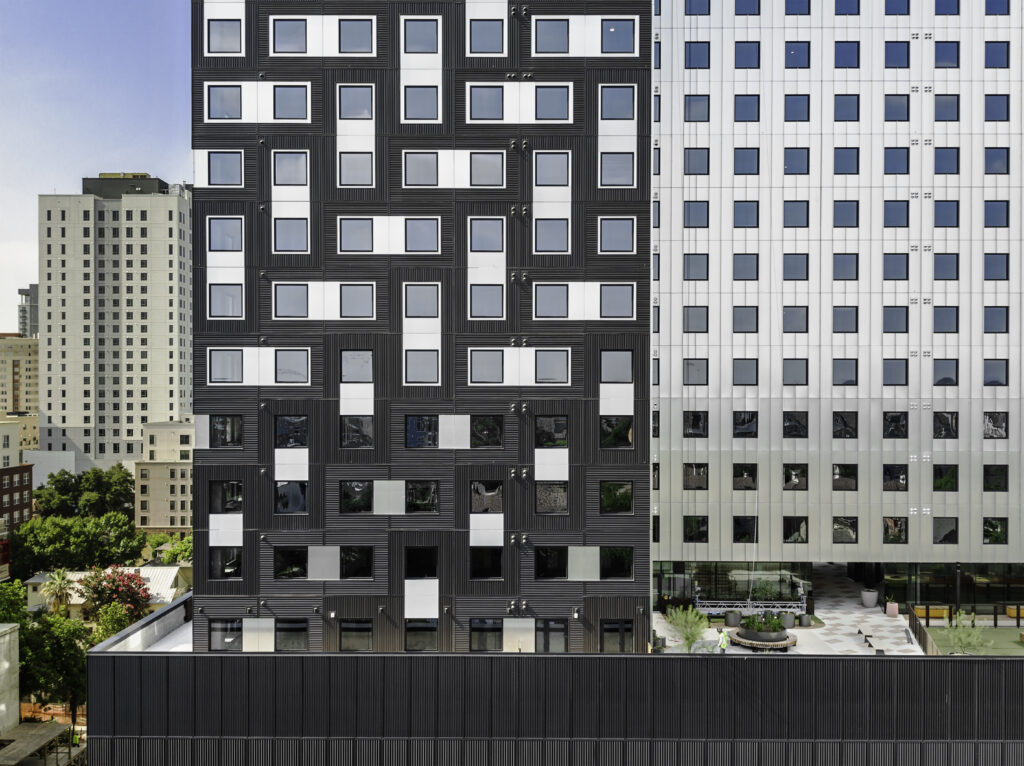
Furthermore, pre-fab construction promotes a reduction in jobsite waste. With components being precisely fabricated offsite, builders can optimize material usage, minimize overages and curtail waste generation during the construction process. This heightened efficiency not only contributes to cost savings but also reduces the environmental burden associated with construction waste. In essence, pre-fab construction positively contributes to greater sustainability and a more environmentally responsible construction industry.
Through the following case studies, we provide a tangible example of the advantages of pre-fab construction, including the benefits realized by the project participants.
The Future is Now: Union on 24th Paves the Way for Prefabricated Excellence
Project Overview
The Union on 24th student housing high rise located on the campus of the University of Texas, Austin, showcases the innovative combination of ALUCOBOND® PLUS aluminum composite material (ACM) and prefabrication construction techniques. Developed by Greystar and constructed with prefabricated panels built by Baker Triangle, the project achieved stunning aesthetics, exceptional quality and an accelerated construction schedule.
The Details
- Location: Union on 24th, Austin, TX
- Project Type: Higher Education, University of Texas, Residential Tower
- Product: ALUCOBOND PLUS, Brushed
- Developer: Greystar
- Fabricator: Baker Triangle Prefab
- Architect: Perkins&Will
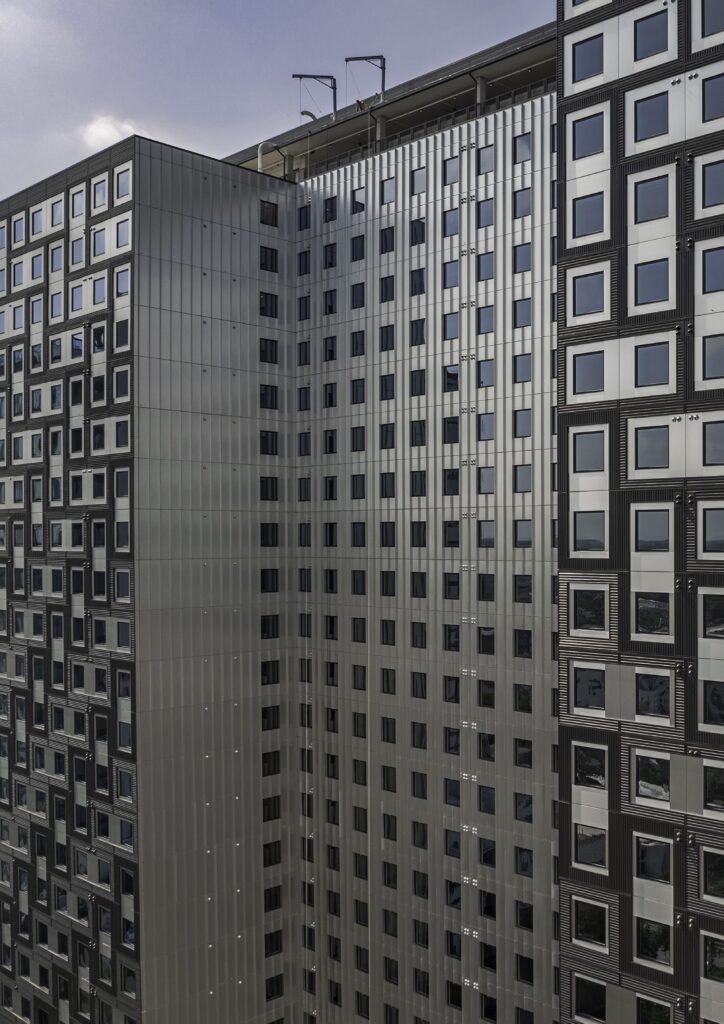
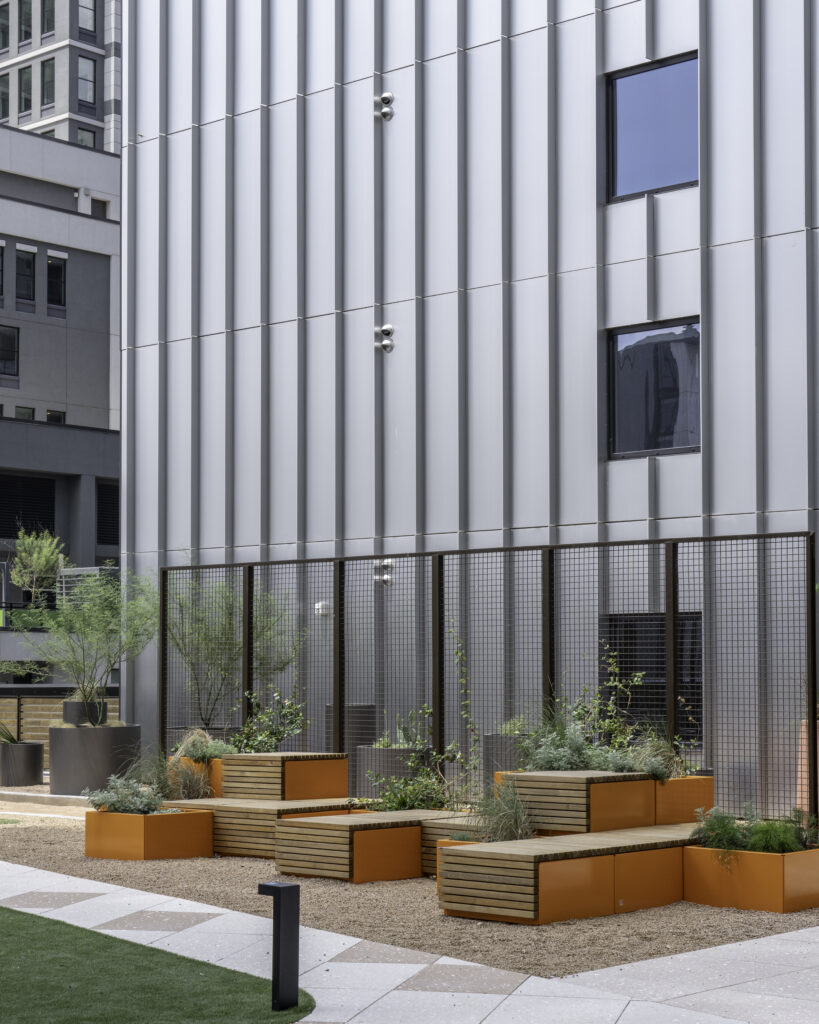
Design
The design of Union on 24th achieves an ideal blend of functionality and visual appeal. A key feature of the building is the ALUCOBOND PLUS panels in “Brushed” finish, which lends a sleek and modern look to the structure. Chosen for its superior formability and consistent appearance, ALUCOBOND PLUS allowed the prefabricated panels to live up to the expectations of the project team. According to Project Manager Clint Bordner from Greystar, “The finished project turned out even better than we hoped,” he said.
The architects at Perkins and Will envisioned a modern and distinctive façade for Union on 24th. Their objective was to deliver a finished look that was both elegant and low-maintenance, and on time. Baker Triangle, recognized the opportunity for prefabrication and proposed the use of Brushed ALUCOBOND® PLUS. This suggestion was met with enthusiasm by the architects and Greystar. The Brushed finish provided a subtle texture, consistent appearance and complemented the other materials used in the building’s design.
Baker Triangle took the concept a step further. They recommended the integration of unique “fins,” fabricated from the same ALUCOBOND® PLUS material. These vertical accents, measuring 6 inches deep, enhance the aesthetic appeal and offer dynamic interest to the structure’s overall look, “The fins are incredibly sleek and beautiful,” noted Sam Balunda, executive vice president, Baker Triangle. “Adding this type of component was a first for us; we couldn’t be happier with how it turned out, it’s a uniquely proud section of the building.”
Fabrication and Installation
The fabrication and installation of the ALUCOBOND PLUS panels was critical to the project’s success, particularly in light of the strict build schedule. Faced with a limited lead time, Baker Triangle’s in-house fabrication capabilities provided a solution that ensured timely delivery and high-quality output. “Prefabricated was my preference and Baker Triangle are the experts,” said Bordner. “With it, everything is much more straightforward – the project moves more quickly, and the quality of the finished panels is top-notch.”
The prefabricated panels were produced at one of Baker Triangle’s 200,000 square foot facilities in Dallas. The panels, measuring 42 by 9 feet, were fabricated, finished and delivered through a just-in-time process, then transported to the jobsite in Austin. This delivery system was crucial in maintaining the project’s pace, with one floor being completed each week.
The installation process was meticulously coordinated with the construction schedule. As the envelop for each floor was finished, the interior work on the floors below were able to be completed by the army of subcontractors involved. This allowed for efficient parallel workflows. According to Greystar, the prefabricated approach saved approximately 12 weeks of construction time, ensuring the project was completed within the required timeline.
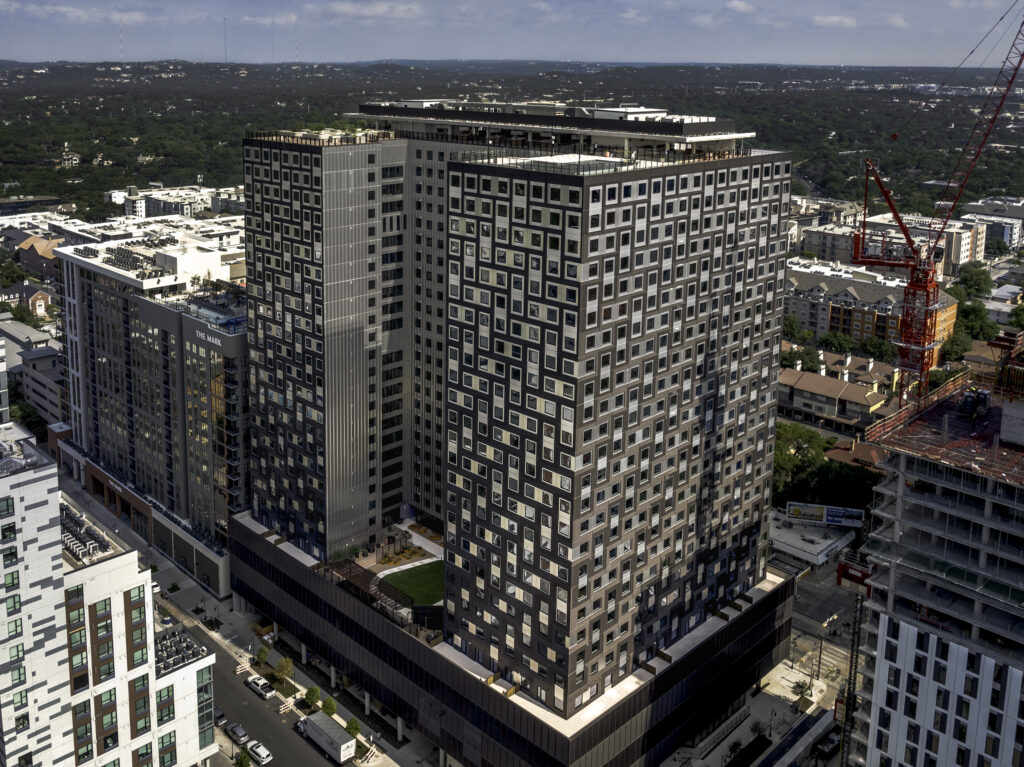
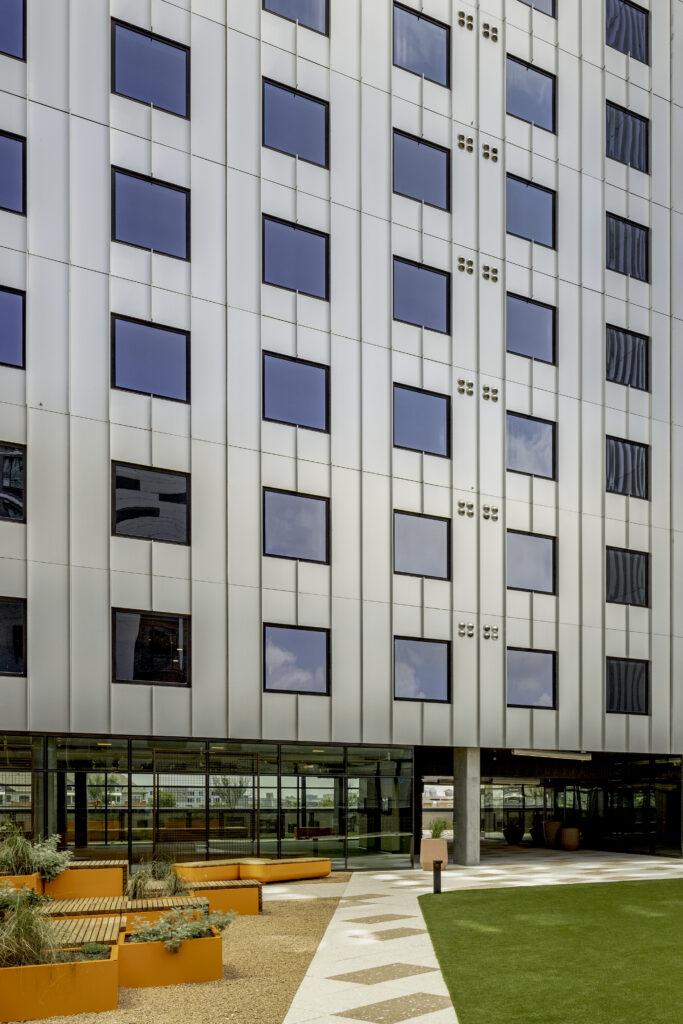
The Quantifiable, Tangible Benefits of Prefabrication
The Union on 24th project serves as a compelling model for the value delivered to projects across education, hospitality and healthcare markets where tight schedules and revenue-generating projects are a priority. Through the use of prefabricated panels constructed with ALUCOBOND® PLUS developers and general contractors benefit from the following:
- Reduced Construction Time: Prefabrication enables the aggressive project schedules. This was a critical advantage for Greystar who need to meet back-to-school deadlines.
- Enhanced Safety: By minimizing on-site labor, prefabrication achieves a dramatic reduction in their Total Recordable Incident Rate (TRIR). This translates to less risk and a safer work environment for all involved. It also contributes to bottom-line savings on insurance premiums.
- Superior Quality: Assembled in controlled environment, such as Baker Triangle’s fabrication facilities, there is greater, more consistent quality control in every panel.
- Design Flexibility: Prefabrication enables expanded design possibilities. For Union on 24th prefabrication allowed for the innovation of the panel fins.
“From a safety perspective, prefabrication is a massive advantage,” explained Sam Balunda, executive vice president, Baker Triangle. “It drastically reduces risk and eliminates the need for extensive scaffolding, which is especially beneficial in a windy city like Austin.“
Possibilities
The success of the Union on 24th project highlights the benefits of prefabrication and the use of ALUCOBOND PLUS in modern construction, demonstrating that combination of material and method can significantly enhance both the quality, efficiency and safety of building projects.
“Prefab construction is the way the industry is going,” stated Balunda. “The ability to enhance design, ensure timely completion and reduce risk makes it a valuable approach.”
Union on 24th stands as a model for the future of construction, where advanced materials and innovative fabrication and assembly techniques can transform architectural visions into reality, efficiently and safely. Greystar and Baker Triangle not only delivered a remarkable building, they set a new industry benchmark, paving the way for a new era in construction, where prefabrication and quality materials like ALUCOBOND PLUS are the cornerstones of success.
The Carson – Elevating Urban Living with ALUCOBOND PLUS
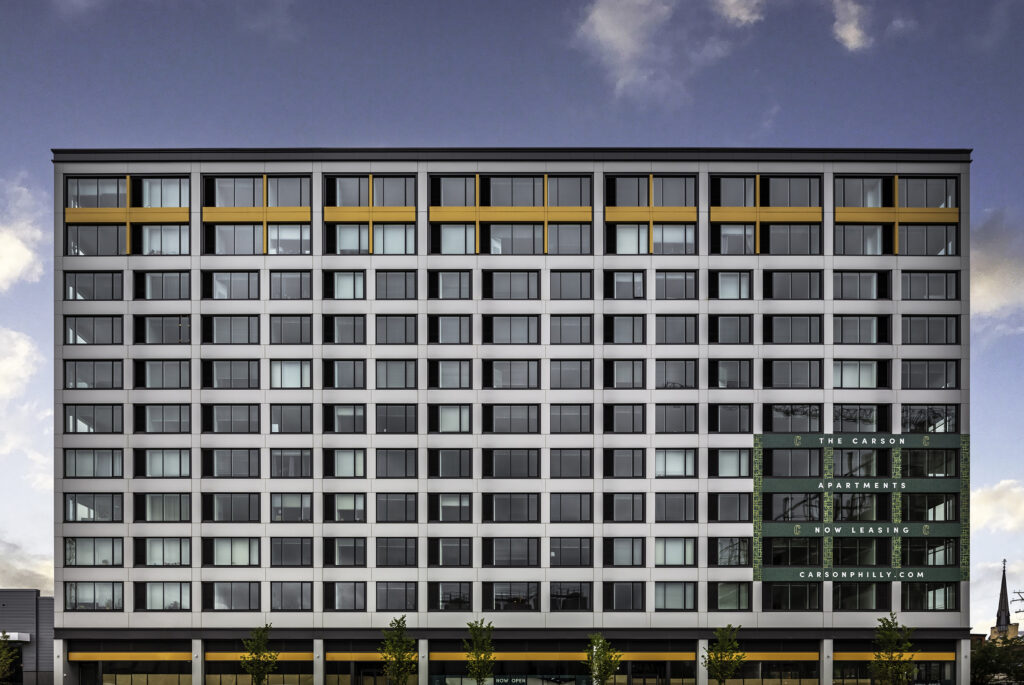
Project Overview
BLT Architects (BLTA) embarked on a transformational project in the Spring Garden corridor of Philadelphia, breathing new life into a worn-down strip mall. From this, the Carson, a 12-story mixed-use development, emerged as a distinctive addition to the evolving urban landscape.
One of the project’s key challenges was to refresh and integrate the existing, outdated one-story grocery store as an anchor structure connecting to the high-rise building while maintaining a sense of architectural harmony. The solution was a c-shaped design, strategically crafting three unique sections, each with its own unique façade, creating a visually appealing and community-friendly structure.
The Details
- Location: 5th and Spring Garden, Philadelphia.
- Project Type: Mixed-use development with residential and commercial units.
- Product: Custom Garden Driftwood, Custom RRM Grey, Custom Great Gray Owl, Spicy Mustard, Custom Electric Lime and Dusty Charcoal
- Metal Panel Fabricator: River Supply, Inc., Brogue, PA
- Prefabricator: Novinger, Harrisburg, PA
- Architect: BLT Architects, a Perkins Eastman Studio
The Design
BLTA’s design goal for The Carson was to create a dynamic and engaging presence within the community – both from the street level and as an element of the city scape. With a backdrop of downtown Philadelphia, the architectural team carefully considered the Spring Garden and 5th Street facades, incorporating design and color elements that give the building dimension and visual interest. The choice of custom ALUCOBOND PLUS colors allowed the design team to be creative and incorporate color, which played a pivotal role in achieving the desired look. In addition, the material’s affordability, durability and adaptability allowed the architects to realize their vision of a modern, urban building that seamlessly integrates into the surrounding community.
“We think a lot about how our designs fit into the urban landscape, and with The Carson we set out to create a building with an attractive street presence, keeping in mind that we were also creating a space that people will call home or think of as a destination,” Zoe Sheaffer, associate, BLT Architects. “By incorporating ALUCOBOND PLUS in custom colors, we were able to reach an ideal balance and complementary palette.”
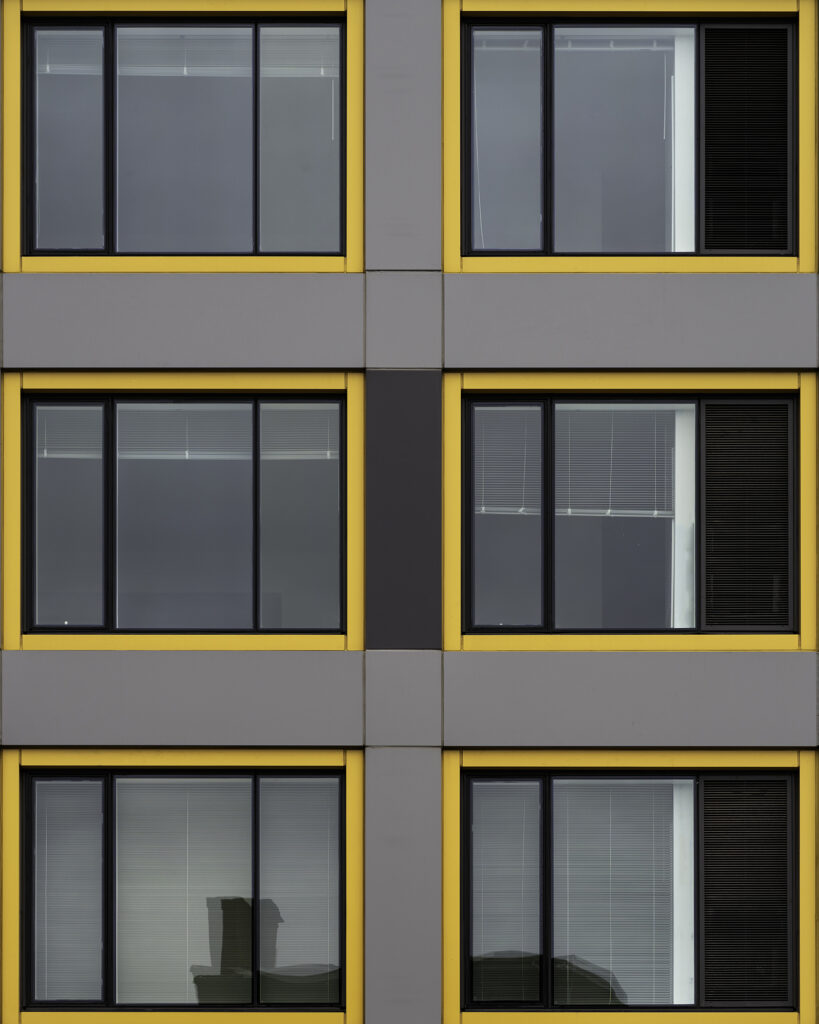
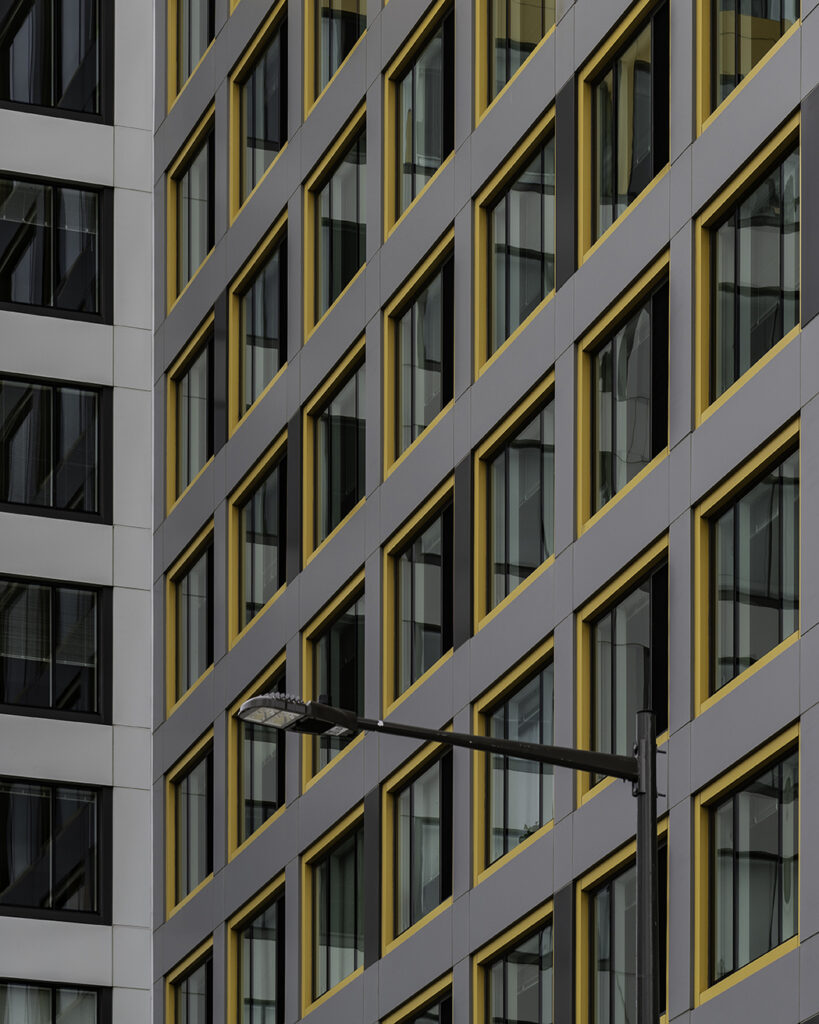
Fabrication and Installation
The successful execution of The Carson project is due in large part to the seamless collaboration between key players — BLTA, River Supply (metal fabricator) and Novinger (specialty contractor constructing the pre-fab panels). BLTA selected ALUCOBOND PLUS for its durability, affordability and design flexibility and their choice was applauded by River Supply and Novinger who were familiar with the material’s efficiency of fabrication, formability and ease of installation.
The two companies — who enjoy a proven track record of partnership — worked closely to streamline the project’s workflow. Novinger, equipped with advanced software, translated the architectural designs into a fully-integrated build plan for nearly 450 horizontal wall sections. This enabled River Supply to create an optimized fabrication strategy that would allow them to achieve the greatest yield and minimize any potential material waste, maximizing cost efficiencies.
While River Supply completed the fabrication of 5,000 individual ALUCOBOND panels, the Novinger team was engaged in building the wall sections — framing out the studs and applying the sheathing, air vapor and insulation. Then, prior to transporting the pre-fab panels to the job site, Novinger finished each of the wall sections by installing the fabricated ALUCOBOND panels. This construction methodology helped to eliminate the typical back-and-forth of a traditional build and expedite the overall project timeline.
The Possibilities
ALUCOBOND PLUS opened up a range of design possibilities for The Carson. Custom colors were carefully chosen to complement the urban aesthetic. The neutral greys of the residential tower provided a sophisticated backdrop, while the dark grey camouflaged mullions. The introduction of Spicy Mustard brought vibrancy to the entryway, contributing to the playfulness of the design. For the anchor grocery store, the designer was able to specify ALUCOBOND PLUS in custom colors to match the brand.
In conclusion, The Carson stands as a testament to the successful fusion of innovative design, the efficiency of pre-fab construction and the versatile application of ALUCOBOND PLUS. This transformative project has helped to revitalize an old space and positively contribute to the local community, offering a contemporary, urban living experience in the heart of Philadelphia.