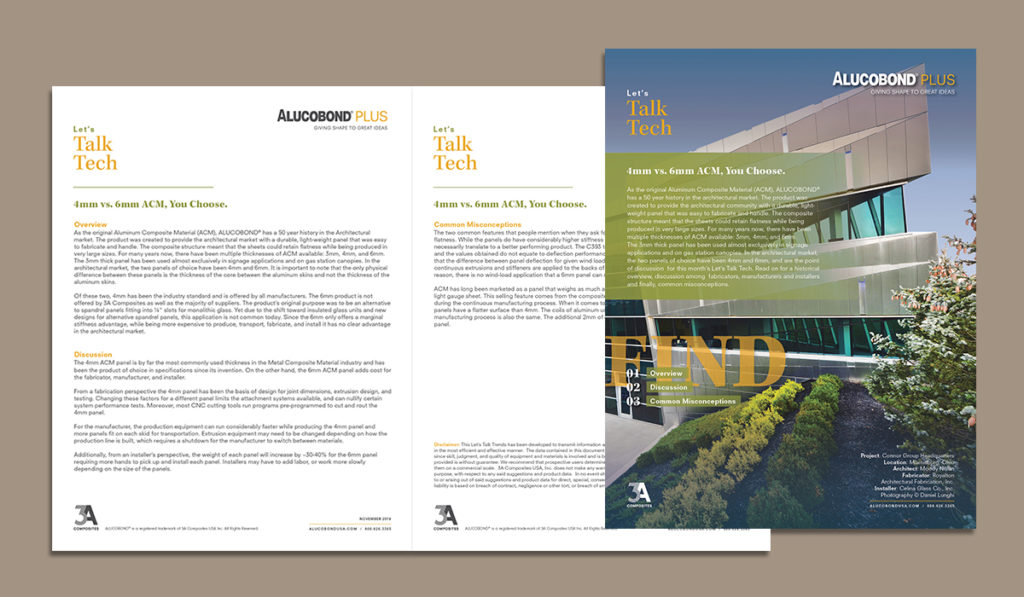
As the original Aluminum Composite Material (ACM), ALUCOBOND® has a 50 year history in the Architectural market. The product was created to provide the architectural market with a durable, light-weight panel that was easy to fabricate and handle. The composite structure meant that the sheets could retain flatness while being produced in very large sizes. For many years now, there have been multiple thicknesses of ACM available: 3mm, 4mm, and 6mm.
PDF Download – Let’s Talk Tech: 4mm vs 6mm
The 3mm thick panel has been used almost exclusively in signage applications and on gas station canopies. In the architectural market, the two panels of choice have been 4mm and 6mm. It is important to note that the only physical difference between these panels is the thickness of the core between the aluminum skins and not the thickness of the
aluminum skins.
Of these two, 4mm has been the industry standard and is offered by all manufacturers. The 6mm product is not offered by 3A Composites as well as the majority of suppliers. The product’s original purpose was to be an alternative to spandrel panels fitting into ¼” slots for monolithic glass. Yet due to the shift toward insulated glass units and new designs for alternative spandrel panels, this application is not common today. Since the 6mm only offers a marginal stiffness advantage, while being more expensive to produce, transport, fabricate, and install it has no clear advantage
in the architectural market.
Discussion
The 4mm ACM panel is by far the most commonly used thickness in the Metal Composite Material industry and has been the product of choice in specifications since its invention. On the other hand, the 6mm ACM panel adds cost for the fabricator, manufacturer, and installer.
From a fabrication perspective the 4mm panel has been the basis of design for joint dimensions, extrusion design, and testing. Changing these factors for a different panel limits the attachment systems available, and can nullify certain system performance tests. Moreover, most CNC cutting tools run programs pre-programmed to cut and rout the 4mm panel.
For the manufacturer, the production equipment can run considerably faster while producing the 4mm panel and more panels fit on each skid for transportation. Extrusion equipment may need to be changed depending on how the production line is built, which requires a shutdown for the manufacturer to switch between materials.
Additionally, from an installer’s perspective, the weight of each panel will increase by ~30-40% for the 6mm panel requiring more hands to pick up and install each panel. Installers may have to add labor, or work more slowly depending on the size of the panels.
Common Misconceptions
The two common features that people mention when they ask for 6mm panels are added stiffness and superior flatness. While the panels do have considerably higher stiffness value per ASTM C393 testing, this value does not necessarily translate to a better performing product. The C393 test is a three point bend tests on a 3” by 8” sample, and the values obtained do not equate to deflection performance of an installed system. ASTM E330 tests show that the difference between panel deflection for given wind loads is within 10%. Installed panels are all framed with continuous extrusions and stiffeners are applied to the backs of all large panels regardless of thickness. For this reason, there is no wind-load application that a 6mm panel can meet that a 4mm panel cannot meet as well.
ACM has long been marketed as a panel that weighs as much as light gauge aluminum sheet, but will not oil-can like light gauge sheet. This selling feature comes from the composite structure of the sheet as well as the tension applied during the continuous manufacturing process. When it comes to flatness, there is no data that shows that 6mm panels have a flatter surface than 4mm. The coils of aluminum used to produce both products are the same and the manufacturing process is also the same. The additional 2mm of core material does not make for a flatter composite panel.
Disclaimer: This Let’s Talk Trends has been developed to transmit information and assist fabricators to work with ALUCOBOND® PLUS materials in the most efficient and effective manner. The data contained in this document is based on information that is, in our opinion, reliable. However, since skill, judgment, and quality of equipment and materials is involved and is beyond the control of 3A Composites USA, Inc., the information provided is without guarantee. We recommend that prospective users determine the suitability of the material and suggestions before adopting them on a commercial scale. 3A Composites USA, Inc. does not make any warranties, express or implied including merchantability and fitness for purpose, with respect to any said suggestions and product data. In no event shall 3A Composites USA, Inc. have any liability in any way related to or arising out of said suggestions and product data for direct, special, consequential or any other damages of any kind regardless whether such liability is based on breach of contract, negligence or other tort, or breach of any warranty, express or implied.