The new Nils K. Nelson Bioscience Innovation Building at Purdue University Northwest has been designed not only to serve as a state-of-the-art teaching facility – housing the university’s college of nursing and department of biological sciences – but as a new “front door” to the 167-acre campus in Hammond, Ind.
Highlights
The $40.5-million facility features a contemporary modular design focused on technologically advanced student learning experiences.
The façade’s material palette was chosen to complement the mid-century architecture on campus that features red/brown brick on buildings while also providing contrast to the heaviness of nearby structures. While the first floor is clad in brick, the upper two floors feature a lighter, more contemporary façade clad with ALUCOBOND® PLUS aluminum composite material.
Shaffner Heaney created detailed shop drawings for the façade panels, incorporating two panel depths and contrasting material between the windows, according to Mark Haab, vice president of operations, Shaffner Heaney Associates, who said the company accommodated this unique metal façade design with a custom extrusion system.
Project: Purdue University Northwest Bioscience Innovation Building
Location: Hammond, Indiana
ALUCOBOND PLUS: Silver Metallic, Brilliant Silver Metallic
Architect: CannonDesign
Fabricator: Shaffner Heaney Associates
Installer: Crown Corr, Inc.
General Contractor: Berglund Construction Co. and Powers & Sons Construction Co. Inc.
Photos: © Mark Kempf Photography
The Project
Located adjacent to the campus’ main parking lot, the three-story 68,000 square-foot Bioscience Innovation Building – which opened in August 2020 as the first new building constructed on campus since 1998 – was designed by the Chicago studio of CannonDesign to be “a striking symbol of forward-looking student space supporting 21st century education,” according to a CannonDesign statement.
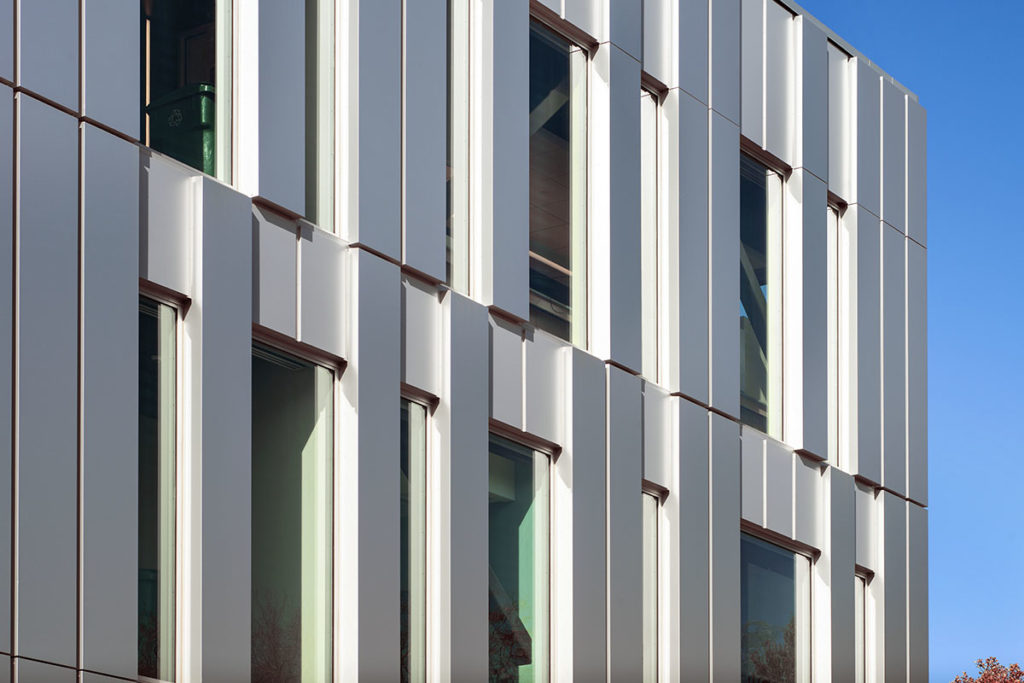
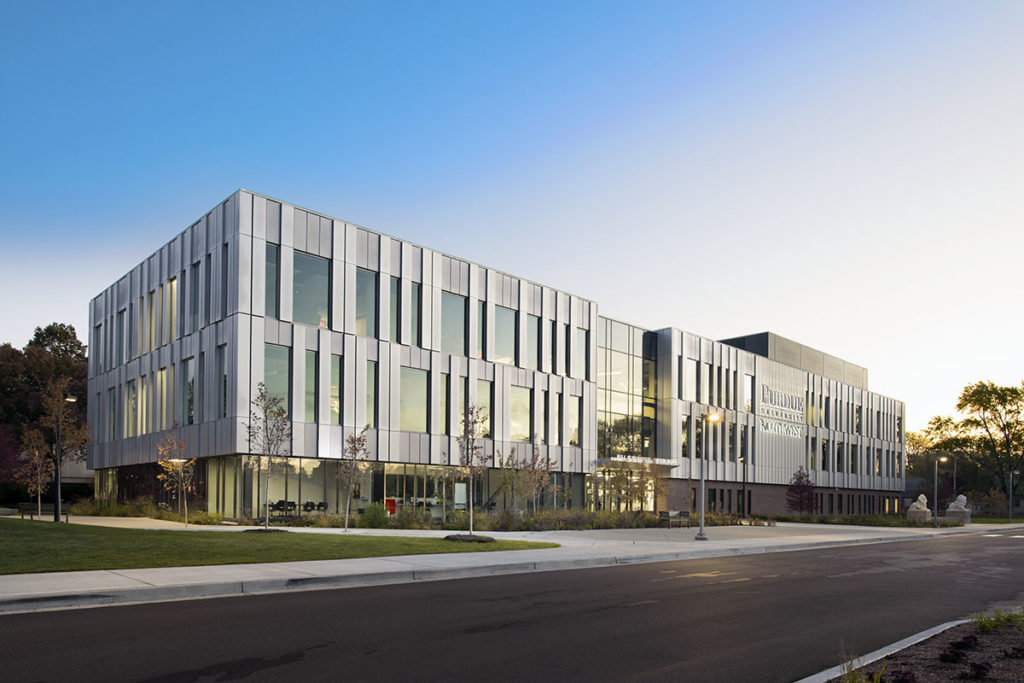
The $40.5-million facility features a contemporary modular design focused on technologically advanced student learning experiences that are showcased through glass-filled classrooms and labs, offering glimpses of today’s STEM learning to science and nonscience-focused students alike. The building’s façade design offers exterior transparency into these programs and interior views back to the surrounding campus.
Design
The façade’s material palette was chosen to complement the mid-century architecture on campus that features red/brown brick on buildings while also providing contrast to the heaviness of nearby structures. While the first floor is clad in brick, the upper two floors feature a lighter, more contemporary façade clad with ALUCOBOND® PLUS aluminum composite material (ACM) by 3A Composites USA and glass.
A total of 24,000 square feet of ALUCOBOND PLUS – including 5,000 square feet of Silver Metallic and 19,000 square feet of Brilliant Silver Metallic both from The Classic Collection – was installed in a modular design on two planes with varying system depths that set off windows. ALUCOBOND PLUS panels were installed in a repeating pattern mixing the Silver Metallic and Brilliant Silver Metallic finishes within wide modules that span the building’s façade. Windows are punched openings within these modules.
CannonDesign reviewed a wide range of silver-hued samples of ALUCOBOND PLUS in the “lighter silver range that would change throughout the day,” according to Brett Lawrence, AIA, LEED AP, associate vice president, CannonDesign in Chicago, who said several flat mock-ups were created to review the ACM samples.
“This is a long building; we wanted to break up the horizontal spans by adjusting the depth of the metal panels and mixing the silver hues,” said Lawrence. “As the sun moves across the side of the building, you see a lot of shadows in the façade.”
In addition to combining two STEM programs, the building was designed to meet the needs of all students who lacked interaction and study spaces on campus and to serve as the university’s new foyer, according to Lawrence.
“This campus has traditionally served commuter students who would sit in their cars between classes,” said Lawrence. “We were called to create more student interaction space within this building. We were able to provide more square footage of this type of space through this program by creating nooks and crannies all over this building for students. … This building is sited at the north end of the university’s main parking lot. We wanted it to become the new front door of the university.”
This new campus “entrance” is marked with “Purdue University Northwest” signature signage attached to a solid area of ALUCOBOND PLUS panels spanning the upper two floors of the building’s façade. “The sign element with metal panels in the background has been well-received,” said Lawrence.
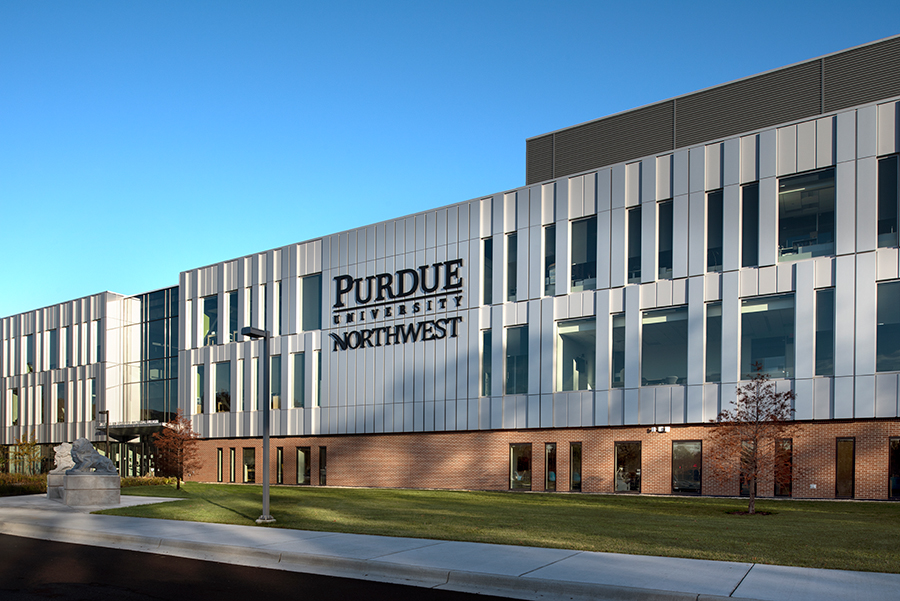
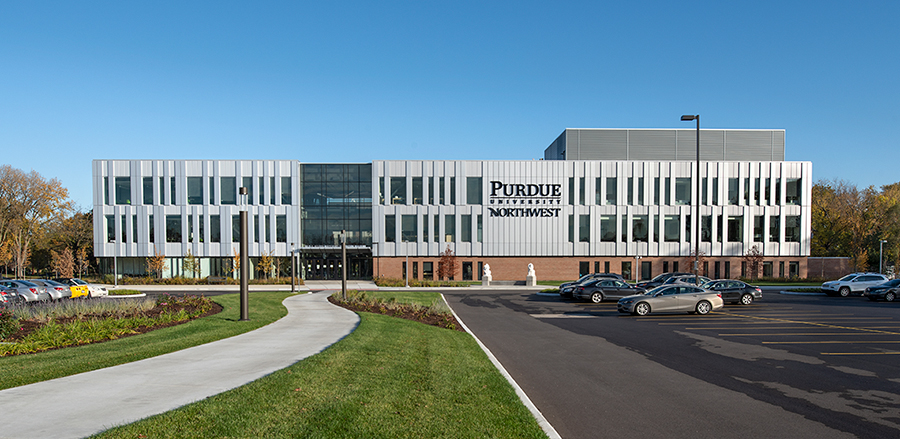
Fabrication
The ALUCOBOND PLUS panels were fabricated by Shaffner Heaney Associates Inc., of South Bend, Ind., and installed by Gary, Ind.-headquartered Crown Corr Inc.. General contracting services were provided by a joint venture between Chicago-headquartered Berglund Construction Co. and Powers & Sons Construction Co. Inc., of Gary, Ind.
“We worked with our ALUCOBOND representative because we wanted to push the boundaries as far as metal panel sizes,” according to Lawrence, who said fabricator Shaffner Heaney “tweaked” the final façade design to achieve maximum performance from the ACM panels.
Shaffner Heaney created detailed shop drawings for the façade panels, incorporating two panel depths and contrasting material between the windows, according to Mark Haab, vice president of operations, Shaffner Heaney Associates, who said the company accommodated this unique metal façade design with a custom extrusion system.
“We drew joint lines at the top and bottom of the windows and recommended that the client add these joints to accommodate material expansion and contraction,” said Haab, who praised ALUCOBOND’s ability to respond to changing material needs.
“The ALUCOBOND worked great on this project; we never have any issues with ALUCOBOND from a cutting standpoint because it’s very flat material,” said Haab. “Service plays a huge role for us in choosing suppliers. We appreciate ALUCOBOND because the company’s sales and customer service representatives are outstanding. That kind of service means a lot; it’s why we prefer to use ALUCOBOND.”
Shaffner Heaney fabricated a total of 1,150 panels ranging in size from 14 feet 4 inches tall by 2 feet wide to 3 feet 4 inches tall by 2 feet wide. The majority of horizontal joints in the material are 1.5 inches wide while vertical joints are 2.5 inches wide – the latter to coincide with the window frame width.
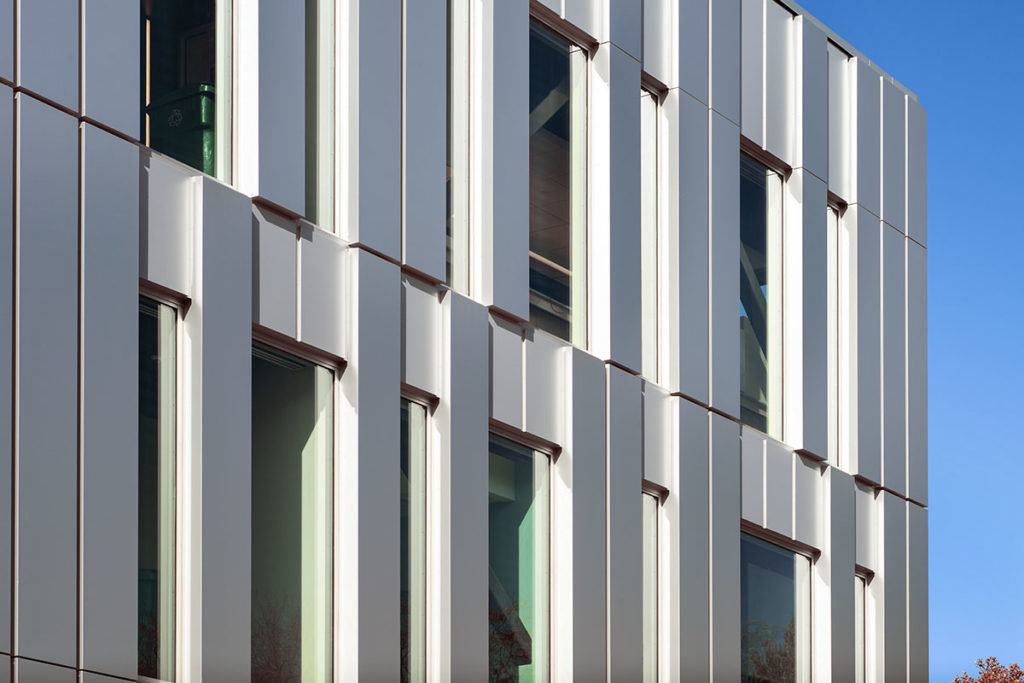
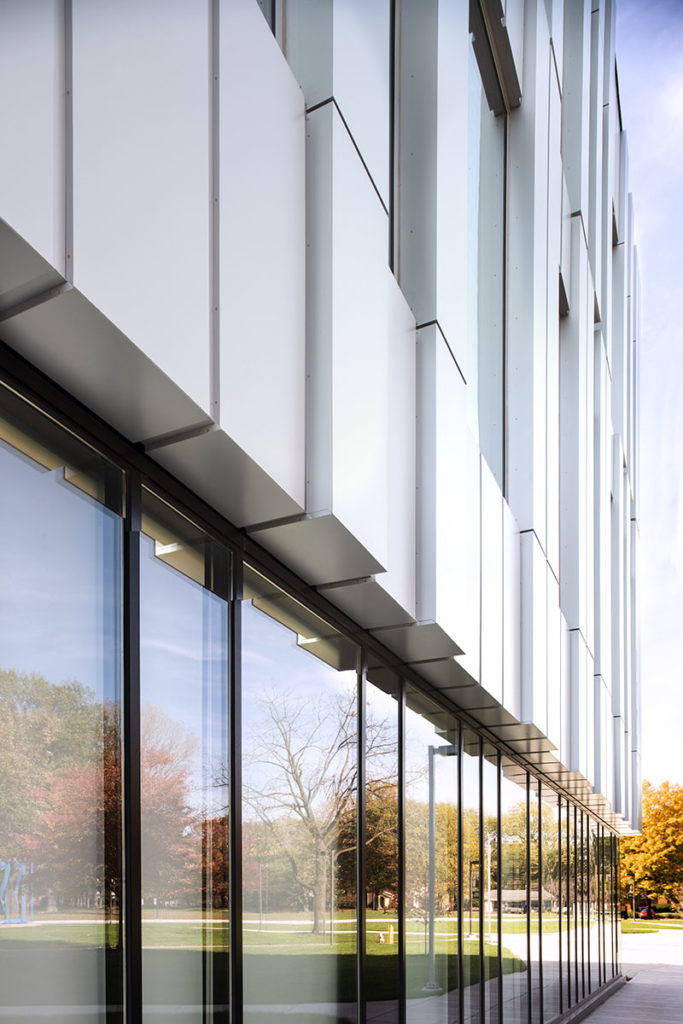
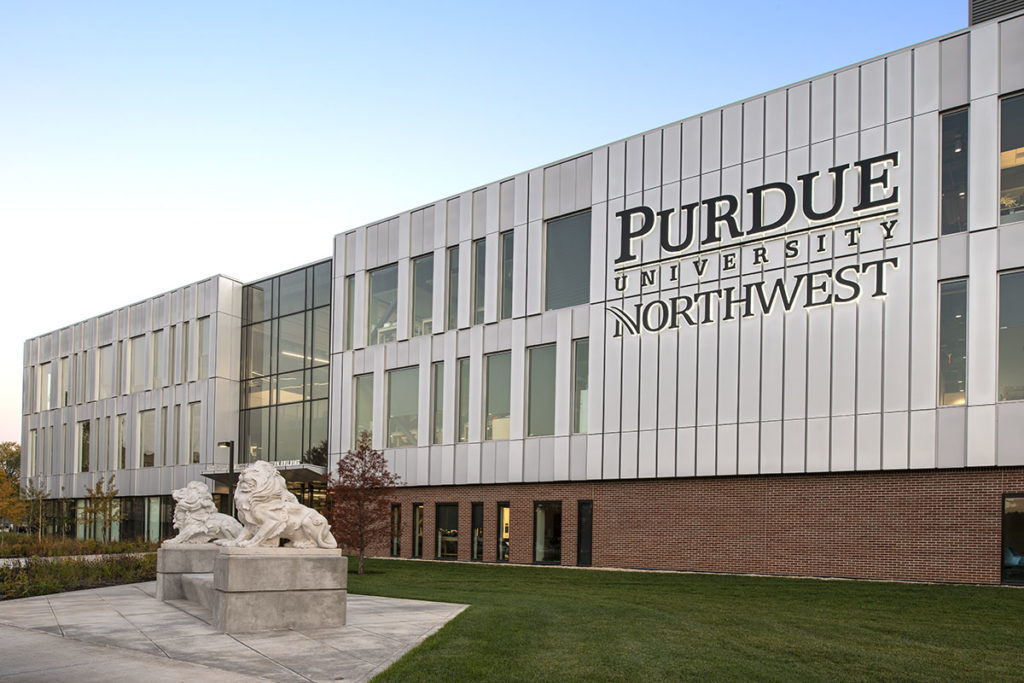
Installer Crown Corr provided precise measurements of the work in place to Shaffner Heaney prior to panel fabrication. Glazing had to be installed prior to panel installation and alignment.
Crown Corr spent approximately six months installing the ALUCOBOND PLUS panels.
“Our original challenge was upfront in the design phase,” said Devin Muzzillo, project manager, Crown Corr. “We worked with Shaffner Heaney and the general contractor to make sure that all of the windows and panels would line up correctly. Our layout had to be correct. Shaffner Heaney did a good job of marking the panels to make sure we installed the colors in the right spots.”
All of the panel layout preparation paid off for the ALUCOBOND PLUS fabricator and installer.
“We were slightly concerned about the complexity of the façade and the ability of the fabricator and installer to execute it efficiently,” said Lawrence. “They did an amazing job on this building. It looks fantastic. Even individuals involved in the inception of this project who doubted that contemporary architecture would be their cup of tea admit that this is a handsome design.”
Muzzillo also is pleased with the completed project.“The metal panels are installed in a unique design with different colors that are really noticeable in the sunlight,” said Muzzillo. “It’s a good-looking building. … We never have issues with ALUCOBOND with any defects. It’s a sharp-looking panel.”